The pure power generated by a hydraulic system is a wonderful thing, but it takes an intricate mixture of proper assembly, maintenance, and proper usage to enjoy its full potential.
And it’s not just about keeping your equipment looking good; we’re talking about saving thousands of dollars by:
- Keeping your hydraulic equipment up and running,
- Avoiding injury and the accompanying costs,
- Achieving more efficiency, and
- Creating a longer lifespan for your equipment.
Imagine having to miss out on a $2,000 job because your hydraulic equipment is down due to the failure of an incorrectly selected or installed hose. Consider the consequences of an employee suffering life-changing injuries simply because the proper use and maintenance rules weren’t put in place. Think about the money you could save by repairing existing equipment instead of purchasing new equipment because of a simple maintenance tip.
With the right procedures and tips on hydraulic system assembly, maintenance, and use, creating a safer environment for your employees while saving your company thousands of dollars could be well within reach.
Hydraulic System Assembly Tips
In order to get the most out of your equipment and avoid downtime, start by selecting the right hydraulic hose for the application. Then, determine the best assembly strategy before finally installing the hose.
Selection
In addition to making sure your hose length allows for some slack when installed, focus on two main factors: working pressure and bend radius.
When a hose is in use, the maximum safe pressure it will support is called working pressure. To avoid equipment downtime and potential operator injury, adhering to working pressure ratings should be a top priority.
Keep in mind that much higher working pressure ratings are typically achieved by hoses with smaller diameters. However, smaller diameter hoses have less capacity to flow larger volumes of fluid and can cause other problems.
Smaller is also better when it comes to bend radius. The smaller the bend radius, the tighter you can safely bend the hose before kinking or other issues distress the hose.
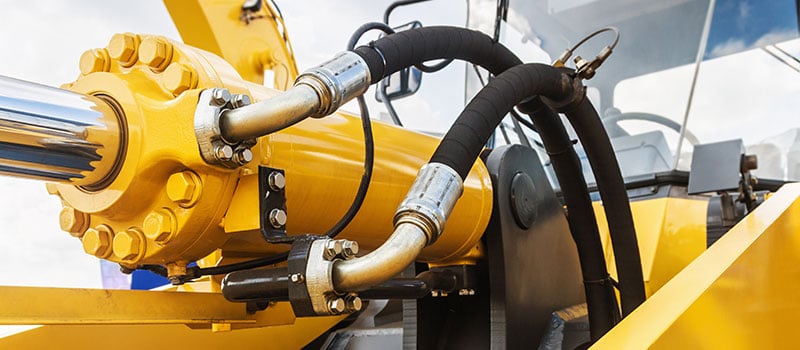
Then, the remainder of your hose selection should come down to STAMP: Size, Temperature, Application, Media, and Pressure.
Size: Note that the inside diameter of the hose is used to determine its official size.
Temperature: Both ambient temperature, the temperature outside the house, and media temperature, the temperature of the media inside the hose, need to be taken into account. Keep in mind that media temperature can have a greater impact on the life of the hose.
Application: We’ll get to hose use later on.
Media: A vital part of hose life is ensuring the inner tube of the hose can work with the media being conveyed.
Pressure: As discussed, focus on working pressure and make sure your hydraulic system pressure does not exceed the working pressure of the hose.
In maintenance applications, you will typically look at the hose already on the equipment and identify it by its SAE number, or other identification, imprinted on the lay line of the hose and use a new hose with the same specifications.
Assembly
Once you have the correct hose in hand, make sure to follow these guidelines for assembly:
As stated in the Society of Automotive Engineers’, or SAE’s, J1273 standard, assembly equipment from one manufacturer is not typically interchangeable with that of another manufacturer. Because of this, do NOT intermix hoses and fixings from two different manufacturers unless you receive explicit written approval or a valid warranty statement.
This means that the best practice when assembling any hydraulic system is to use any hose, fittings, and crimper from the same manufacturer. This is how we typically do things in the United States - in the rest of the world, hydraulic hose, fittings, and crimping equipment from all different manufacturers work together as long as the proper crimp specifications are followed.
Then, follow the manufacturer’s guide for assembly.
Installation
Lastly, it’s time to install the hose. To avoid equipment downtime and injury, be sure to implement these installation tips:
- The hose will change in length when pressure is applied, so be sure to provide slack that will allow for changes of +2% to -4%.
- Twisting can cause a number of problems for a hydraulic hose, so follow the lay line on the hose during installation to avoid twisting - use swivel hose ends on at least one end to prevent twisting during installation.
- Route the hoses away from sharp edges and hot parts or insulate them to protect from the heat.
- To avoid collapses and kinks, keep the bend radius of the hoses as large as possible.
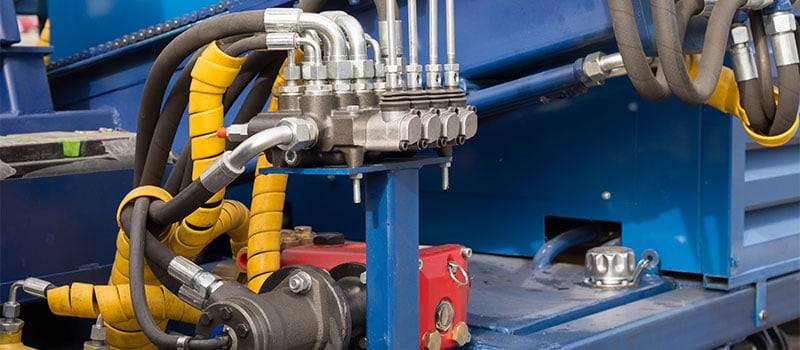
With assembly covered, let’s move on to maintenance.
Hydraulic System Maintenance Tips
Why suffer the loss of business from hydraulic system failure when a simple maintenance procedure could have spotted your problem and allowed for an easy fix?
Here’s how to properly inspect and maintain your equipment:
The first part of the maintenance process is the alertness of hydraulic system operators. Being aware of when equipment looks, sounds, smells, or feels different in daily operation is the first line of defense against system failures.
Regularly scheduled inspections should also be a part of your maintenance program, so be sure to refer to the inspection recommendations of the equipment manufacturer.
When conducting inspections, use the following checklist to best prevent hydraulic system failure:
- Start by turning off the equipment.
- Release the pressure from all hoses.
- Place the equipment in a neutral position.
- Allow the equipment to cool down.
- Inspect hoses and fittings by looking for leaks, kinking, twisting, lack of slack, proximity to heat sources, abrasions, hardness, discoloration, or a generally dirty appearance.
- Take the necessary steps to fix any issues by replacing the hose, adding insulation, replacing fittings, or any other necessary course of action.
- Inspect the valves, pump, and cylinders of the hydraulic equipment.
- Reinstall all parts and turn the power back on.
The vast majority of hydraulic hose assemblies are produced using crimped on hose ends -although screw together (reusable) hose ends are still used in some markets.
Companies maintaining a large number of equipment using hydraulic hose often have an inhouse crimping system to allow them to produce their own hydraulic hose assemblies and help avoid costly equipment downtime.
Proper maintenance of these crimping systems is just as important as maintain other hydraulic equipment.
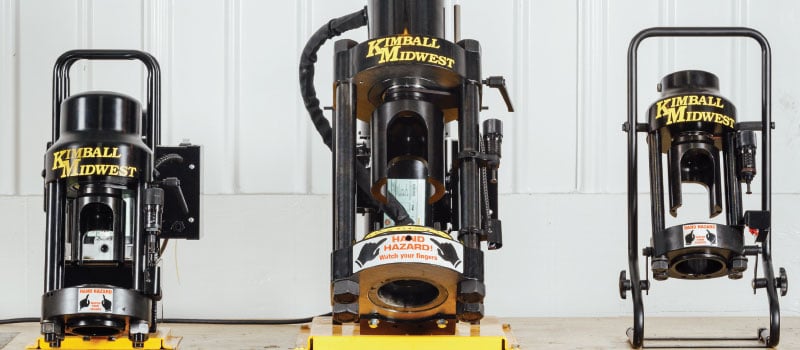
So, let’s move on to the maintenance of your crimper, the hydraulic ram used to crimp fittings onto hose:
- A high-pressure grease should be regularly applied to the inside surface of the die bowl.
- On occasion, clean out the grease in the die bowl entirely before adding a fresh layer.
- Conduct regular inspections of the crimper for cracks, chips, etc. in the pusher, collets, and pressure plates or spacer rings.
- The inspection should also include a close look at the hose connection between the crimper and pump.
- Repair/replace any necessary parts if a failure is found in steps 3 and 4.
- Check for normal ram force. If ram force is lower than normal, a fitting will not be crimping to its nominal crimp diameter - which you can measure for. Check the oil reservoir level and look for leaks. If no issue is found, check the pump seals for wear. Replace any parts as necessary.
- After every 40th crimp, measure the nominal crimp diameter against the manufacturer’s specification chart to ensure the right sizing.
When all of the above is complete you’ve completed the maintenance check of your equipment and crimper.
Benefits of Maintenance
The most important benefit is ensuring your equipment will operate at a safe and efficient manner at all times. This allows you to avoid unnecessary injury and unplanned rework.
You’ll also limit the unscheduled equipment downtime due to failure that can lead to missing deadlines, less-than-perfect quality, and losing opportunities for new business.
These maintenance procedures will also keep your equipment replacement rate low, avoiding the significant repair costs brought on by major failures.
Extending the lifetime of your equipment is another benefit, a clear and obvious money-saver by delaying the time between purchasing new equipment.
Finally, these maintenance procedures promote safety from things like leaks and fluid spills, which can lead to issues with the Environmental Protection Agency, or EPA.
And although the assembly and maintenance tips you’ve received thus far can go a long way towards saving your company thousands on their own, we’re not done yet.
Hydraulic System Usage Tips
When it comes to any hydraulic system, safety is the top priority. So, we’ll start with some precautionary measures before moving on to some specific tips for using hoses within your hydraulic setup.
Safety Precautions
From extremely hot temperatures, to significant physical forces, to poisonous fluids, any hydraulic equipment operator must be aware of the potential dangers of the job.
These are the most notable hazards:
- Pinhole leaks and injection hazards
- Hose whipping
- Burns
And the prevention of these hazards includes its own benefits, including the safety of employees, less time spent on unscheduled emergency work, and money saved by not having to repair critically damaged equipment.
Pinhole leaks and injection hazards
In the case of pinhole leak injections, any operator must be particularly alert to the hidden danger. A pinhole leak injection occurs when a microscopic leak is created in a hydraulic system hose, which consequently injects hydraulic fluid into skin when an operator runs his or her hand along the hose in search of a leak.
The most hazardous part of this injury is that although poisonous fluid has been injected into the body, there’s very minimal pain felt at the point of contact. However, because our bodies can’t process the hydraulic fluid, injuries can quickly become severe by the time any significant pain is felt within a few hours.
According to a 2008 case report titled, “High-pressure injection injury of the hand: an often underestimated trauma: case report with study of the literature,” the most dangerous part of this injury, “is hidden behind a small and frequently painless punctiform skin lesion on the finger or the hand. These kinds of injuries require prompt surgical intervention with surgical debridement of all ischemic tissue.”
Without immediate medical attention, a pinhole leak injection can lead to the loss of the finger, hand, or arm.
To prevent pinhole leak injections, the hand should NEVER be used to locate a hose leak. Instead, a piece of thick material should be used to check for leaks while the operator also wears chemical-resistant gloves.
If a pinhole leak injection is suspected, seek medical attention immediately.
Hose whipping
The potential for injury from forceful impact due to hose whipping is also a potential hazard of hydraulic systems. When pressure causes a fitting to separate, the hose can become loose and whip violently. The force of this whipping hose has the ability to cause real harm to an operator, and to equipment.
To prevent hose whipping, conduct regular inspections of the hydraulic system equipment and properly maintain all aspects of the machinery.
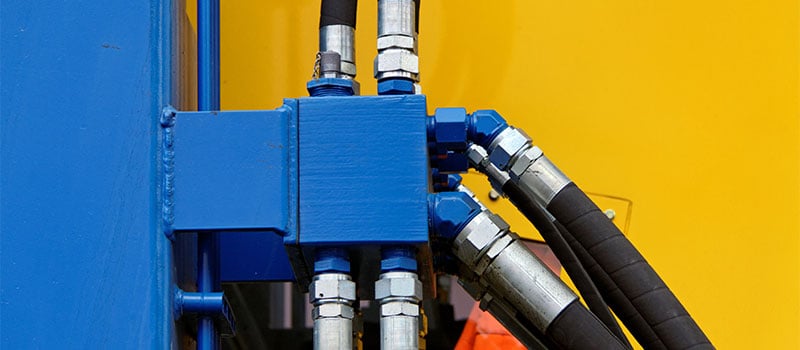
Burns
An operating hydraulic system can result in very hot hydraulic fluid, which presents the danger of burn injuries if the fluid comes in contact with the operator. The most potential for this injury to occur is if a hose end blows off - which is a catastrophic failure.
This hazard is just another reason to perform regular inspections of hydraulic equipment in order to prevent injury.
Hose Usage
Depending on the maintenance of a hose, its lifespan can be drastically shortened or lengthened. So, let’s cover what you should avoid and what you should implement in order to achieve the most favorable conditions for your hoses.
First, the shelf life of a hose can be shortened when exposed to heat and/or moisture. To keep the shelf life of the hose at a maximum length, keep the hose in its original packaging until you’re ready to use it.
When in use, avoid premature failure of the hose by adhering to the following guidelines:
- Keep the system pressure below the rated working pressure of the hose. This can prevent wear and tear on the hose.
- Keep the working temperature below the maximum working fluid temperature of the hose.
- Avoid working in extremely low ambient temperatures. When this is unavoidable, special low temperature hoses may be required to prevent stiffening and cracking.
- Although different hoses have different bend radii, avoid bending as much as possible to prevent any potential physical damage.
- Twisting can be much more damaging to the hose than bending, so refrain from twisting in all circumstances. Unlike bending, hoses are not made to twist at all, so twisting can dramatically shorten the life of a hose.
When you implement the above tips for hose usage, you can reap the rewards of higher efficiency and fewer replacement parts. Plus, you’ll have a safer hydraulic system setup to give you peace of mind.
From assembly to maintenance to usage, you can save thousands of dollars by keeping your equipment up and running and avoiding injury with these hydraulics system safety and maintenance tips.
Are you ready to start using this information but don’t know where to begin? Let Kimball Midwest do it for you!
Thanks to the Kimball Midwest Experience, we can offer:
- Reduced downtime
- Improved productivity
- More efficient use of maintenance personnel
- Customized hydraulics parts inventory
- Fast identification of hydraulic parts
- Decreased safety hazards and accidents
- Extended equipment service life
- Reduced new equipment expenses
Plus, we can increase the efficiency and safety of your maintenance hydraulics operation with inventory organization, parts standardization, and the elimination of obsolete inventory. 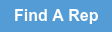
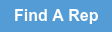