Jobs that require abrasives in your shop may seem overwhelming. There are so many abrasive products that you can choose from, and you don’t want to ruin the material you’re working on. So how do you know which abrasive to pick?
In simple terms, abrasives can be broken down into two categories. Coated abrasives (sandpaper, abrasive cloth rolls, and flap discs) and bonded abrasives (grinding wheels, cut-off wheels, and other solid abrasive products). Coated abrasives have a cloth or paper backing that has abrasive grain bonded onto its surface. Bonded abrasives contain abrasive grain held together in a matrix of binders with the grain dispersed throughout the material.
Application
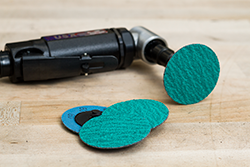
1. Cutting
2. Grinding
3. Finishing
2. Grinding
3. Finishing
Cutting
Cutting abrasive products are used to remove material either by cutting through a thin cross section of the material, removing a limited amount of the base stock. Cutting wheels are thin and allow you to quickly cut through materials like steel, stainless steel, and other metals. The thinner the wheel, the faster the cut.
Grinding
Grinding Wheels: A grinding wheel is a bonded abrasive meant for use on an angle grinder or bench grinder. There are heavy duty products that are capable of removing base stock quickly, but depending upon the abrasive grain, can also be used for finishing applications.
Griding Discs: These are a coated abrasive and run the range from larger resin fiber discs to small 1/2-turn on 1/2-turn off quick change discs. They are used in a wide range of applications such as grinding, finishing, and polishing. Their specific job depends on the grit size and abrasive grain.
Finishing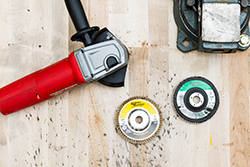
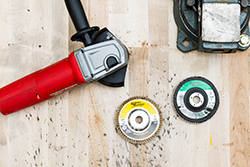
While finishing products are also abrasives, they have a different use than the first two categories. Finishing abrasives are for cleaning, polishing, and removing paints and coatings. Finishing abrasives include surface conditioning discs, surface preparation wheels, emery cloth, and a variety of fine grit products. They come in sheets, rolls, and discs.
Grit
The grit size defines how large the abrasive grains are. In general, the larger the abrasive grain, the more aggressive the abrasive action will be as the grain takes a larger bite out of the base stock.
Grit
The grit size defines how large the abrasive grains are. In general, the larger the abrasive grain, the more aggressive the abrasive action will be as the grain takes a larger bite out of the base stock.
Grain
Abrasives can also be separated by the type of grain used. Abrasive grain is what allows the disc or wheel to remove stock or provide the final finish.
The three most common types of grains are:
The three most common types of grains are:
1. Ceramic
2. Zirconia
3. Aluminum Oxide
2. Zirconia
3. Aluminum Oxide
Ceramic Grain
Ceramic grain is typically the most aggressive and provides the longest service life. In action, it is tough and less brittle than other abrasive grain. Ceramic requires more pressure to allow it to fracture to expose fresh, sharp edges for cutting, so it is used in the toughest applications.
Zirconia Grain
Zirconia is a high performance grain that is also tough and durable but will fracture at a lower pressure than ceramic grain. It is ideal for heavy duty grinding and cutting, but also more general purpose applications. Depending upon the design and construction, abrasive products made with zirconia grain may not last as long or work as quickly as those made with ceramic grain.
Aluminum Oxide
Aluminum oxide is one of the original high performance grains and is often blended with ceramic and zirconia grain for a more economical product. Aluminum oxide is an excellent general purpose abrasive grain. While products made with aluminum oxide grain may not last as long as those made with ceramic or zirconia, they provide good service life combine with economy in use.
It should be noted that no matter the abrasive product and grain you are using, you must take precaution as abrasive wheels can be dangerous. If the disc or wheel cracks and you use it on your grinder, you run the risk of it flying apart. If you drop an abrasive wheel on the ground or notice a crack, throw it away and get a new one. Safety glasses and gloves are never be optional when using abrasives.
Abrasives are a vital part of your shop, so understanding what discs or wheels should be used for certain applications is important. While there is more to abrasives than application and the grain used, now you won’t be abrasive when it comes to using your abrasives.
Learn more about our extensive line of abrasives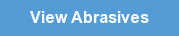
Learn more about our extensive line of abrasives
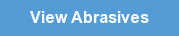