Hydraulic Hose Assembly Preventative Maintenance
From airplanes to snow plows, hydraulic hose assemblies are present in our everyday lives. They are responsible for carrying fluids under pressures up to 10,000 pounds per square inch and with temperatures up to 300 degrees Fahrenheit. Additionally, these assemblies perform their very important jobs in hostile conditions. They endure harsh temperatures and weather conditions, on top of the normal bending and flexing of the hoses.
Since about 50% of hydraulic system downtime can be traced to hose or coupling failures, it’s obvious preventing these failures can save thousands of dollars in downtime.
Before any work can be performed, the proper steps must be followed to ensure safety.
- Release system pressure by powering down the equipment.
- Check the pressure gauge. It should read 0 PSI. This ensures the accumulators are released of pressure as well.
- Use a lockout/tagout procedure. This sequence of safety procedures will prevent injury by guaranteeing the person who started and is carrying out the work is the only person who can restore energy to the system.
- Damage to hose, such as abrasion, bulges, color change, hardness, crushed hose, and scuffs.
- Indicators of leaks, like oil or dirt around fittings and along the hose or even puddles of hydraulic fluid.
- Routing issues such as twists or kinks in the hose. It also is important to pay close attention to potential hazards that could damage a hose – it should avoid high temperature and abrasion from nearby components.
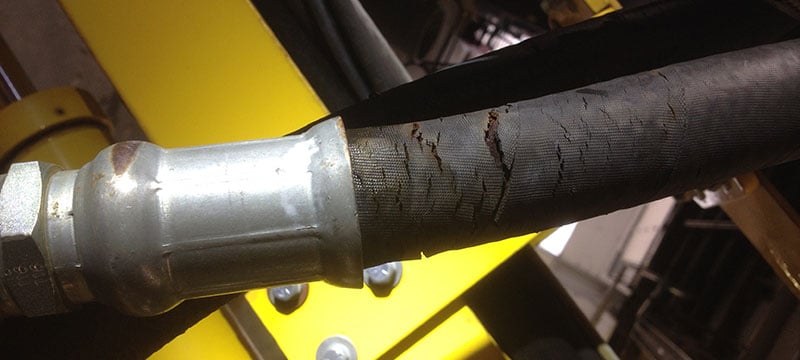
When all fixes and replacements are complete, ensure the access panels are placed properly back in their positions, then carry out the rest of the lockout/tagout procedure.
Crimper Preventative Maintenance
Crimpers are large investments that can, in the long run, save a business lots of money. However, they do require a certain amount of attention. If cared for, crimpers should last a long time.
Crimper Maintenance Checklist:
- Regularly apply a high-pressure grease to the inside surface of the die bowl or cone. Wear on dies or collets can lead to out-of-spec crimps.
- When a crimper is used in a dirty and dusty environment, occasionally clean out existing grease in the bowl and provide a fresh layer.
- Use a high-grade hydraulic oil and maintain its level to within ½” of the top of the reservoir.
- Inspect the dies or collets for any chips or cracks.
- As you would inspect other hose assemblies, check the assembly connecting the pump to the crimper as discussed above.
- Confirm there are no leaks around the piston and cylinder.
- The nominal crimp diameter should be measured for every hose assembly created. Match the measurement with the manufacturer’s crimp specification chart to ensure proper finished crimp diameters.
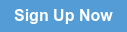